Le stock de calories (eau "morte")
Ce stock a pour vocation de garder l'excédent de calories pour la restituer plus tard. Ça, c'est la théorie, dans la pratique c'est un peu plus complexe.
J'ai constaté après un certain temps de fonctionnement que :
-
d'avril à octobre : il y a assez de calories pour pouvoir les stoker
-
de novembre à mars : il vaut mieux "pomper" les calories dans le stock en temps réel
Ce dernier point n'est pas forcément évident à faire en fonction des conceptions hydrauliques faites. Effectivement, un circuit de chauffage maison est un circuit fermé pressurisé alors qu'en drainback, le stock est ouvert et à pression atmosphérique constante. Le seul moyen est donc de passer par un échangeur thermique à l'intérieur.
Conséquence de ce choix, pour pomper en temps réel les calories, il faut que le stock soit déjà à une température minimum et ça, en hiver, c'est pas gagné car il y a peu de soleil !
Je pense que le drainback n'est valable que si votre chauffage central est conçu déjà en basse température (type plancher chauffant) sinon en hiver c'est quasiment mission impossible (peut être possible dans le sud ... et encore).
Personnellement, en hiver par les températures chez nous, je n'utilise le stock que pour maintenir les dalles en température durant une belle journée. Ceci nécessite un stock déjà à un minimum de 30°C en partie haute. Voici la conception de mon stock :
-
1500L (emprise au sol de l'eau de 0.93m x 0.93m ...... du stock fini isolé de 1.4m x 1.4m)
-
hauteur d'eau à 20°C = 1.73m
-
hauteur d'eau à 80°C = 1.78m
-
ossature bois (calculée pour une poussée de 1.35Tonnes) avec double étanchéité EPDM intérieure
-
isolation de 20cm de laine de roche
-
échangeur thermique composé de 4 radiateurs suspendus en partie haute branchés en parallèle
-
1 canne d'aspiration froide basse et 1 canne de refoulement chaude haute (ce qui permet de bien stratifier la cuve)
-
Le tout sanglé par acquis de conscience par 2 sangles d'une tonne de traction chacune.
-
4 sondes TH pilotantes (en haut, mi-haut, mi-bas et en bas).

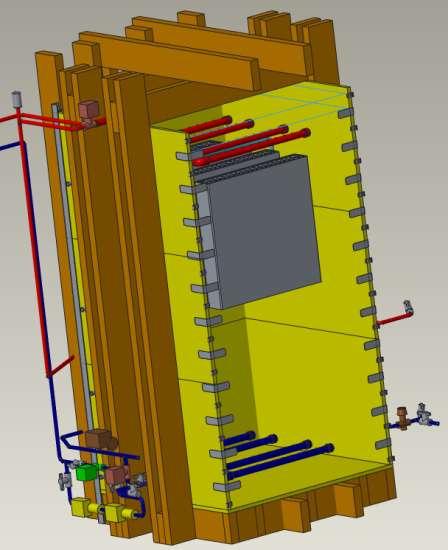
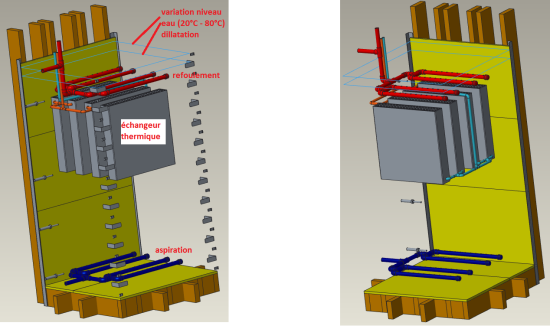
J'ai choisi de fabriquer le stock in-situ pour la simple raison que je ne pouvais pas passer avec un ballon tampon du commerce. Il aurait fallu en mettre 2 en parallèles et c'est plus difficile à gérer ensuite.
Avantages :
-
on lui donne presque la forme voulue
-
s'adapte à la place disponible
-
satisfaction personnelle
Inconvénients :
-
bien calculer la poussée (voir plus bas)
-
pas de garantie fabriquant
-
NE PAS SE TROMPER DANS LE CALCUL DE L'EXPANSION DU VOLUME D'EAU A HAUTE TEMPÉRATURE (cf coefficient de dilatation de l'eau plus bas)
La porte avant est ouvrante pour intervention technique.
La hauteur de dilatation de l'eau dans le stock
Comme on est à pression atmosphérique constante, lors de la chauffe c'est le volume de l'eau qui augmente. Il faut donc calculer cette différence de hauteur pour dimensionner la hauteur finale du stock.
Voici les coefficients de dilatation de l'eau :
D'après le pdf ci-dessus et en considérant que je limite la température de l'eau du stock à 80°C :
-
ΔV =1500l x (0.02899 - 0.00177) = 40.83 litres d'expansion
-
Donc : ΔH = ΔV / (0.93 x 0.93) = 0.04083 m3 / (0.93m x 0.93m) = 0.047m = environ 5cm
-
hauteur finale stock = 173cm + 5cm = 178cm ...... fixée au final à 1m80
Lors du premier remplissage, veillez à bien mettre une hauteur d'eau de 1m73 maxi à 20°C ! ! ! ! !
L'effort de poussée et logiciel de dimensionnement LIBRE
L'effort de poussée
Cet effort de poussée n'est pas constant en fonction de la hauteur mais variable. C'est une fonction de :
-
la hauteur
-
la masse volumique du fluide et son centre de gravité
-
les dimensions de la paroi
Soit le cas de figure suivant :
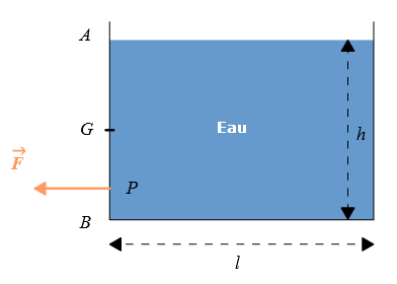
L'effort F de la poussée sera :
F = ρ.g.ZG.S
ce qui donne finalement :
F = ρ.g.(h/2).(h.l)
-
F en newton (N) : à savoir que 10N = 1Kg environ
-
ρ en (Kg/m3) : pour l'eau ρ = 1000 Kg/m3
-
h & l en (m) : dépend des dimensions
-
g = 10 m/s² (pesanteur terrestre)
Le centre de poussé Zp se situe au 1/3 de la hauteur en partant du bas.
Par conséquent, chacun des 4 bastings verticaux reprend environ :
1350 kg/ 6 = 225 kg (et oui, les 2 coins reprennent également le 1/6ème de l'effort environ)
J'obtiens une déformation maxi de 4mm en flexion sans dépasser la résistance à la rupture du matériau (du pin).
Le logiciel de résistance des matériaux LIBRE
Il se prénomme "freelem" et est téléchrageable ici :
http://www.freelem.com/telechargement/
Les cannes et la stratification
Dans un ballon ECS classique, on rempli par le bas (le plus lentement possible) et on pompe par le haut. Ceci a pour effet de stratifier la cuve et de ne pas obtenir de l'eau mélangée tiède. Lisez ce document fort intéressant sur le sujet :
Dans mon cas, c'est l'inverse, c'est de l'eau chaude qui va rentrer et de l'eau "froide" qui va être pompée. Il est tout à fait logique que la canne de refoulement se situe en haut et que la canne d'aspiration se situe en bas sachant que l'eau chaude est plus légère que l'eau froide !.
Il ne reste plus qu'à prévoir une forme qui permette un remplissage avec la vitesse la plus faible possible pour conserver la stratification ...... CQFD !
Cela fonctionne super bien et je constate (en analysant les 4 sondes TH) qu'elle stratifie parfaitement. Même si elle se dé-stratifie lorsque l'on pompe les calories à l'intérieur via l'échangeur, au prochain chauffage solaire, cela se re-stratifie sans problème.
Calcul de la vitesse de sortie de l'eau par les trous des cannes
Avec un débit solaire total de 800 l/h, j'obtiens une vitesse de sortie de l'eau des trous de 3.3 cm/s.
Depuis, je suis passé à 600 l/h et donc la vitesse en plus faible.
Notez toutefois que tous les trous n'ont pas le même débit en réalité.
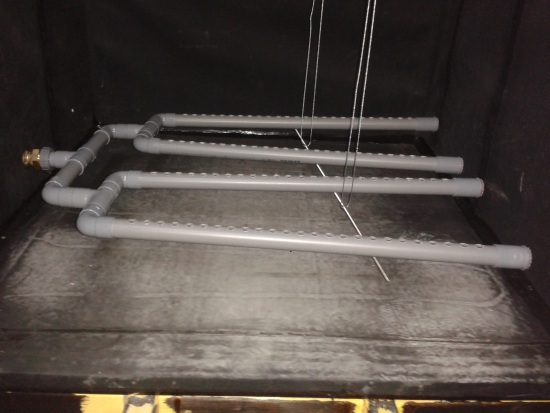
On large rondelle de pression en inox (non représentée) vient en appui avec la bâche d'étanchéité avec un joint de colle pour EPDM :
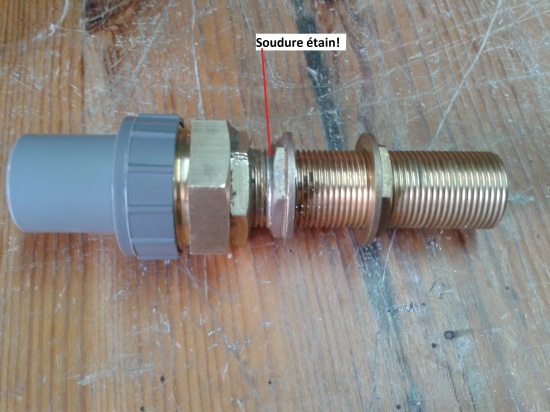
Les trous des deux cannes doivent être orientés vers le haut pour favoriser la purge de l'air !
La réalisation et l'étanchéité
L'étanchéité est réalisée par bâche en EPDM qui résiste à 140°C :
-
La première est découpée et collée sur les parois internes
-
La deuxième est d'une pièce, centrée au fond et soigneusement pliée à l'intérieur pour garantir l'étanchéité.
La première qui est collée
Le bois est un matériau vivant et fibré. Il est naturellement chargé d'humidité. Lorsqu'a eu lieu la première montée en température aux alentours de 70°C, il s'est asséché et donc contracté.
Conséquence directe :
-
contraction du bois
-
apparition de fentes plus ou moins marquées (certaines peuvent atteindre jusqu'à 1cm de large).
Cette première couche n'a qu'un objectif :
-
éviter que la deuxième bâche ne forme des bourrelets au travers de ces fentes les plus larges.
Je n'est pas eu le réflexe de prendre des photos malheureusement.
L'échangeur thermique N°1
L'échangeur thermique est directement plongé dans la partie haute du stock. Il permet la récupération des calories. Plutôt que de réaliser un échangeur classique en cuivre tel qu'on peut les connaître, j'ai choisi d'imiter un échangeur à plaque.
J'y ai plonger 4 radiateurs montés en parallèle. Ils sont suspendus :
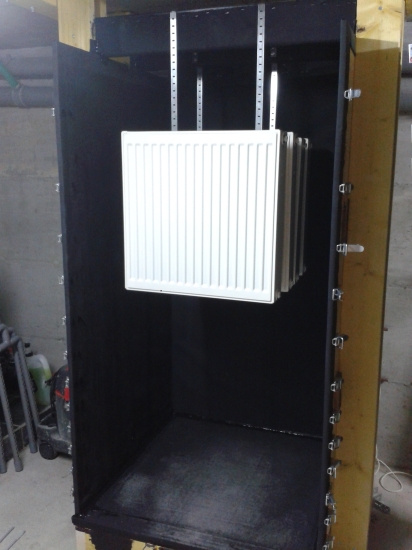
AVANTAGES :
-
bon captage des calories sur toute la section de la cuve (si bien dimensionné)
-
débit du fluide divisé par 4 si la distribution est bien faite
INCONVÉNIENTS :
-
lourd (dans mon cas au total environ 100 à 120 kg le tout)
-
4 suspentes en inox (20mm x 3mm x 1m)
Je suis obligé de passer par un échangeur thermique car le fluide solaire est à pression atmosphérique constante alors que le circuit de chauffage maison & piscine (2ème échangeur tubulaire lui) sont sous pression.
Et oui, s'il n'y a pas assez de soleil, j'ai la possibilité de chauffer ma piscine avec la géothermie de la maison d'où un circuit pressurisé.
Dimensionnement
Le problème réside dans le fait que le cuivre et l'acier (radiateurs) n'ont pas la même conductibilité thermique :
-
cuivre : environ 390 W/m/K (à 20°C)
-
acier : environ 46 W/m/K (à 20°C)
d'où un facteur de 8 à 9.
Une règle empirique (mais qui me paraît correcte) dit que la surface d'échange de l'échangeur cuivre plongé dans le stock doit représenter de 20% à 30% de la surface totale des capteurs en toiture.
Dans mon cas avec 16m² de capteurs :
-
20% = 3.2 m² de surface d'échange en cuivre
-
30% = 4.8 m² de surface d'échange en cuivre
Prenons une moyenne de 4 m² de surface d'échange en cuivre(épaisseur tube de 1mm)
Ceci nous ramène donc à une surface d'échange en acier de 32 m² à 36 m² (facteur multiplicateur de 8 à 9).
J'utilise 4 radiateurs (double ailettes) de 60cm x 60cm x 10cm.
Donc pour un radiateur :
-
S1 = 0.6 x 0.6 x 4 = 1.44 m² (2 surfaces ext + 2 surfaces int = 4)
-
S2 = 0.08 x 2 x 48 x 0.6 = 4.62 m² (48 ailettes de 0.08 m le longueur développée sur 0.6 m de haut et sur 2 faces)
-
S = S1 + S2 = 6.06 m² / radiateur
-
S total = 4 x S = 4 x 6 = 24 m²(soit un facteur multiplicateur de 6 au lieu de 8 à 9)
De toute façon, pas le choix, je ne peux pas mettre plus gros. En prenant 3.2 m² de surface d'échange en cuivre (20%), on arrive à un coefficient multiplicateur de 8, moi ça me va.
Après mise en service, l'échangeur fonctionne très bien.
Réalisation
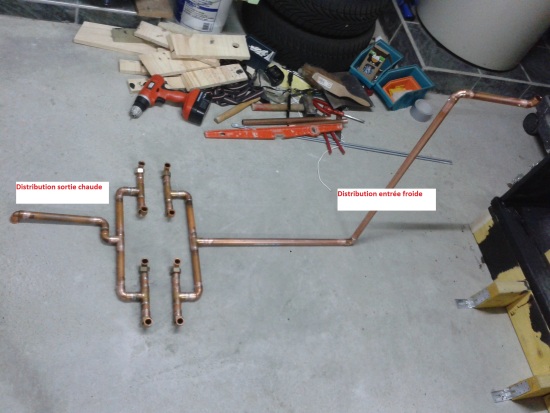
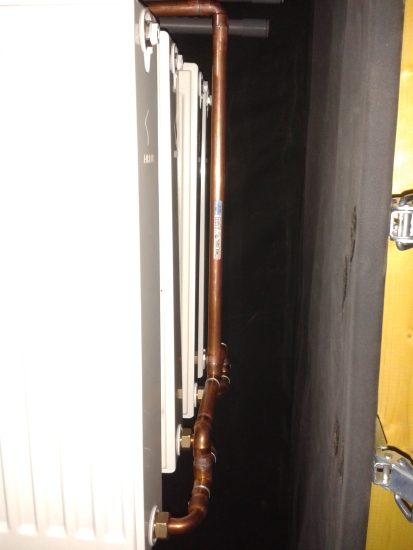
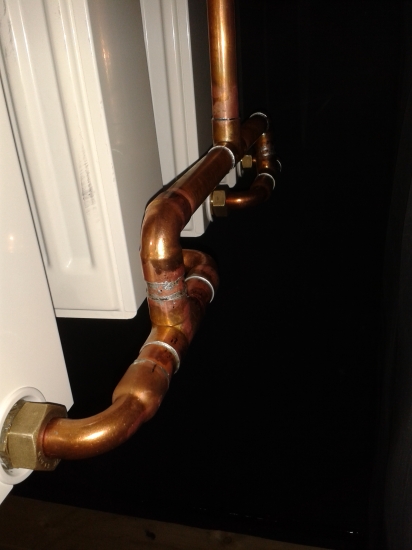
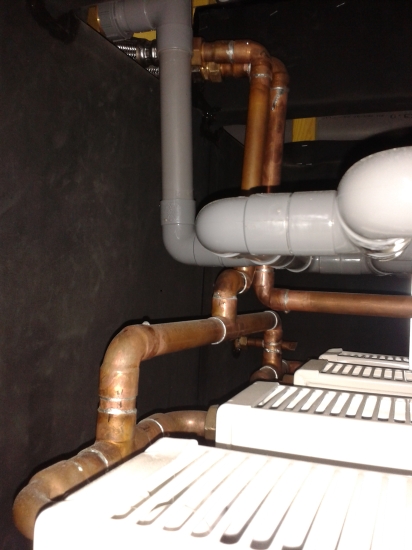
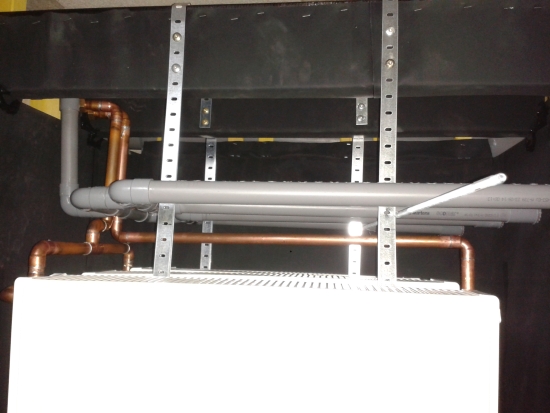
Les suspentes initiales (acier zingué) étaient là pour tester le tout sur quelques mois. Je vais les changer pour de l'inox (fer plat 20 x 3 x 1000 (en mm)).
L'échangeur thermique N°2
En voulant changer mes suspentes pour de l'inox, une sacrée surprise m'est tombée dessus !
Lorsque que j'ai ouvert mon stock, une sacrée couche de rouille était déposée au fond et tout l'EPDM était souillé !
Honnêtement, je m'attendais à la corrosion mais pas aussi vite ! ! !
L'origine du problème
Seuls deux éléments pouvaient engendrer de la rouille :
-
les corps et fonte des circulateurs
-
les radiateurs suspendus dans le stock
Évidement c'était les radiateurs. J'avais lu plusieurs témoignages sur le net concernant cette solution assez plaisante car rapide à faire. Cependant, aucun n'a mentionné ce problème .... s'en sont-ils au moins rendu compte ? Ont-ils peut-être des radiateurs en aluminium (je ne pense pas que ce soit une bonne solution) ?
Le constat étant fait, la seule solution viable est de passer par un échangeur cuivre comme prévu initial en utilisant la distribution existante :
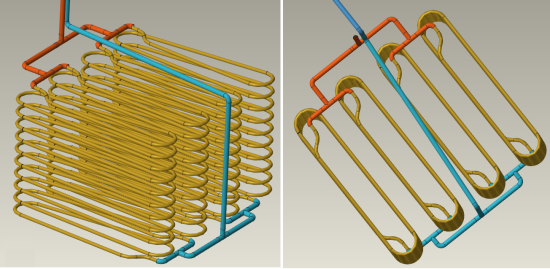
La solution corrective
L'échange de chaleur se fait dans ce cas par convection. Les calculs peuvent être menés en prenant en compte ce document (extraits d'un ouvrage de mécanique appliquée) :
Notions de transfert thermique
La relation donnée dans la section "convection" peut être transformée de la manière suivante :
-
ΔQ/Δt = puissance P (kW)
-
k = 0.5 (coefficient dans le cas le plus défavorable)
-
S = π x Øtube x lgtube (surface réelle d'échange thermique en m²)
-
Δθ = différence de température entre le stock et le fluide de l'échangeur (°C)
Donc on a :
P = k x (3.14 x Øtube x lgtube) x Δθ
Dans mon cas :
-
Calcul de la puissance calorique souhaitée :
Je souhaite pomper dans mon stock de 1500l un deltaT de 20°C (50°C - 30°C) en 6hrs (ce qui est pas mal en plancher et radiateur basse température). J'obtiens donc :
Énergie = P x t = 1.16 x 1500 x 20
Donc :
P = (1.16 x 1500 x 20) / 6 = 5.8 kW ...... que j'arrondis à 6kW (c'est comme si j'avais une résistance électrique de 6kW).
-
Calcul de la surface S d'échange thermique :
Je choisi du cuivre recuit de diamètre Øext = 14mm (c'est le plus couramment utilisé et donc le moins coûteux à l'achat). Il a l'avantage aussi de se travailler assez facilement avec ou sans outillage (tout dépend de ce que l'on veut faire).
Je prends un Δθ = 6°C. On aura donc :
lgtube = P / (3.14 x 0.014 x 0.5 x 6) = 46m (soit une surface d'échange S = 3.14 x 0.014 x 46 = 2.02 m²)
-
Choix de la surface S d'échange thermique finale :
Je choisi de mettre 4 spires en parallèle de 15m de long (ce qui correspond à 4 couronnes du commerce à la bonne longueur), soit 60m de tube et donc S = 2.63 m²).
Mon circuit de chauffage rentre dans le stock en Ø20/22mm en cuivre, ce qui fait une section de passage du fluide de :
s = 3.14 x (20/2)² = 314 mm²
Avec 4 passages en Ø12/14mm, la section totale de passage du même fluide est de :
s = 4 x 3.14 x (12/2)² = 452 mm²
Conclusion : mon échangeur ne freine pas la circulation du fluide de chauffage.
Concernant la réalisation, plutôt que de faire des spires ovales, j'ai réalisé des spires rondes (facile à former à la main). Il y en a quatre montées en parallèle.
Avantages :
-
on lui donne la forme voulue
-
débit divisé par 4 dans mon cas (et donc des pertes de charges limitées).
-
échangeur plus compact pour le positionné en partie supérieure (là où l'eau est chaude)
-
plus facile à mettre en place (masse)
Inconvénients :
-
ne pas faire de plis francs au risque de percer le cuivre
-
trouver un moyen de suspendre les spires (pour moi 4 fers plats en inox avec quatre tiges filetées elles aussi en inox sur lesquelles les spires reposent)
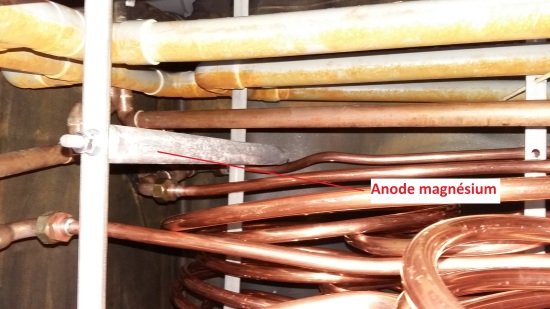
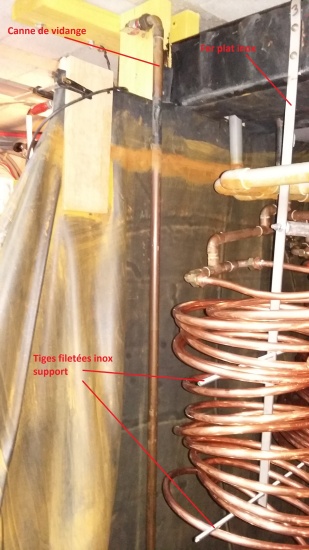
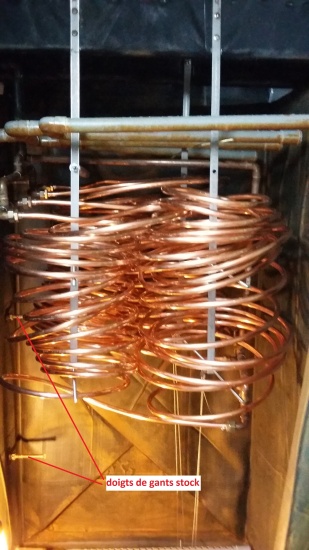
Après sa mise en service, CELA FONCTIONNE MIEUX QU'AVANT !
Donc préférez un échangeur cuivre ! !
L'isolation
Elle est assez classique, 20cm de laine de verre avec habillage final de propreté :
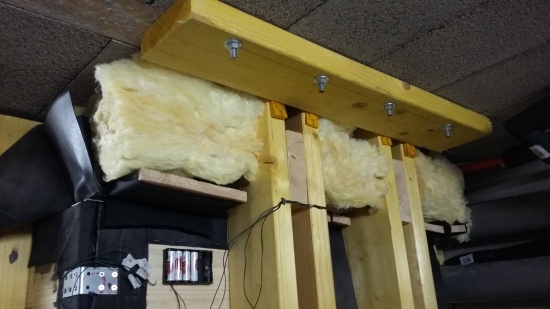
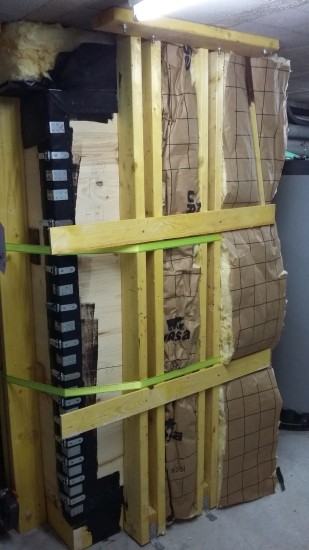
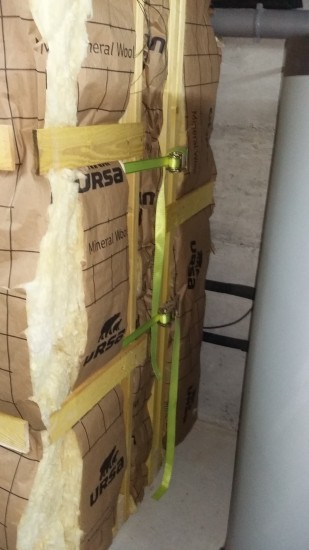
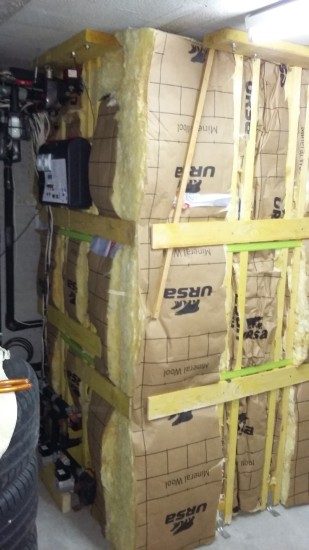
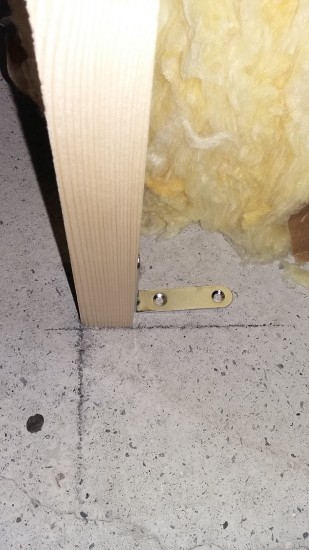
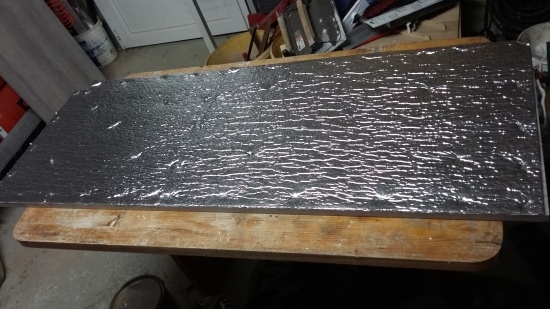
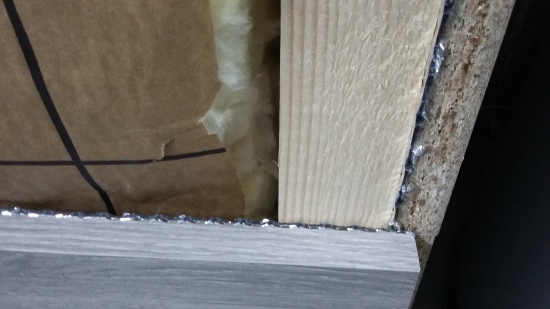

Le PC n'est là que pour de la supervision, le système est totalement indépendant pour fonctionner.
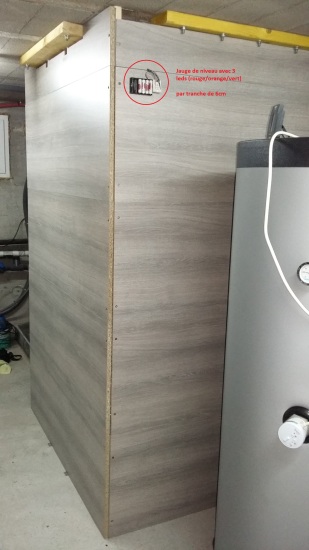